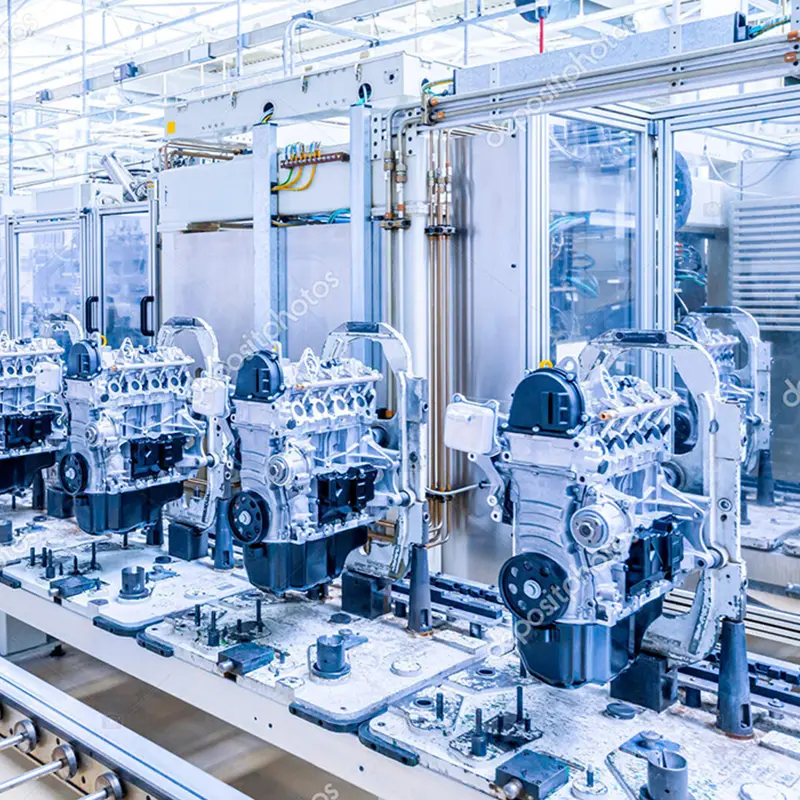
Improved Product Quality
Ensures only products that meet quality standards reach the customer.
Reduced Waste
Early detection of defects can prevent defective products from reaching the end of the line.
Cost Savings
Reducing the cost of recalls and rework.
Customer Satisfaction
Delivering high-quality products enhances brand reputation and customer satisfaction.